The phrase is getting used more and more, but is a ‘modular home’ one that a house-hunter should seriously consider buying? Any mental image of prefab property of the 1940s and 1950s should be set aside when it comes to the standard of homes built off-site these days.
Homes built in pieces somewhere and brought ‘ready-made’ to a site became best-known in the UK after the Second World War, where they helped meet the urgent need for dwellings to replace those which were bombed. Intended as temporary, with a lifespan of up to ten years, a large number these 150,000 or so ‘prefab’ homes built up to 1951 remained in use for many years, even decades. There are still some lived in even now.
Post-war prefab homes were basic and renowned for poor design and quality standards, the type to avoid unless there was nothing else available. Even several generations on from the war, many consider the idea of building a home in a factory and delivering it to a site in the same way, but the homes which a built off-site today are a world away from those of 70 years ago.
Modular housing is one of the things which the industry believes will help tackle Britain’s urgent need for new homes, particularly at the affordable end of the market. More housebuilders are turning to off-site construction and there are major benefits to this.
- Quality control: everything has to meet stringent standards before it is even allowed to leave the factory.
- Speed of build: construction time is significantly reduced by using completed elements of a building in the construction process.
- Price: requiring less time and fewer people to build means significantly reduced costs which can help make a brand new modular home more affordable to would-be buyers on a limited income than those built on site in the traditional way.
- Energy efficiency: the advanced technology of building offsite improves air-tightness and energy consumption, a plus for homeowners’ bills and the environment as a whole. Completion of these homes onsite requires fewer man-made products and fuels than traditional building.
It has taken the UK a long time to start embracing the offsite construction of its much-needed new homes. Richard Payne, director of development at specialist lender Oblix Capital, recently said: “Compared with other parts of the world, the UK has been remarkably slow in adopting the construction method – in Japan, 15% of houses are built using prefabricated elements, in Germany, the figure is 20% and in Sweden, the figure is a remarkable 84%. In 2017, it was estimated that c15,000 modular homes are constructed in the UK each year (which is less than 10% of all dwellings completed during 2017).”
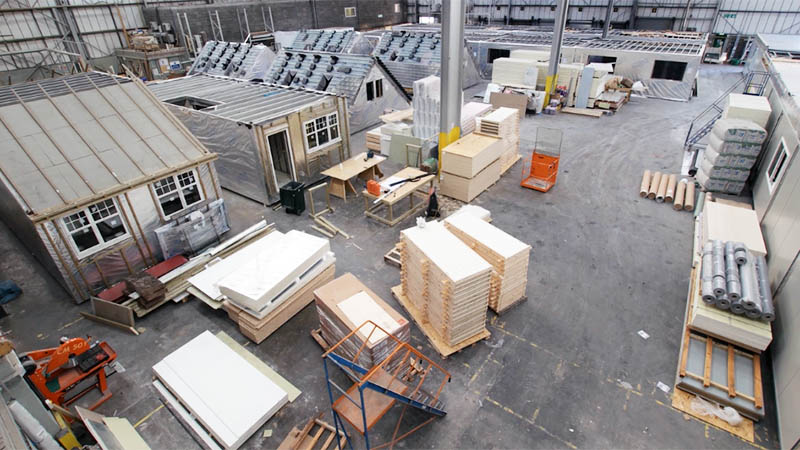
Here's a time-lapse video of Flagship Group's modular construction process.
But there are certainly some significant examples right now, where various degrees of the project are being delivered to the site pre-constructed.
Positive Homes is an environmentally focused housebuilder that produces very energy-efficient homes and recently worked with Yorkshire-based specialists ilke Homes to deliver nine zero-carbon homes to Newark, Nottinghamshire, and they are so convinced of the eco-credentials of this method of construction that they will producing only modular homes in the future.
A new phase of homes was recently released at Port Loop in Birmingham. These 28 townhouses will be built offsite and on selected plots, only the size of the properties has been predetermined – buyers will be able to make a choice from some 70 internal floorplans. to suit their own lifestyle. Guy Ackernley, head of residential sales for the Port Loop Joint Venture, said: “Once designed, the house is built in our factory and then craned onto site, ready for final decorations. As well as offering greater flexibility, this construction method helps minimise any defects and ensures a higher-quality, and often quicker, build process.”
Planning permission was recently approved for the second phase of the major Northstowe project, creating a new town of 10,000 new homes in Cambridgeshire. The new village of Inholm comprises 406 modular homes, the majority of which will be manufactured in Urban Splash’s House factory in Alfreton, East Midlands. Mark Latham, regeneration director at House said: “We are offering a range of customisable homes and apartments to suit a wide range of modern families, lifestyles and budgets. We can’t wait to get going.”
Well underway is a major development in Bedfordshire. Strawberry Star’s LU2ON, just 200m from Luton Airport Parkway station, is providing 758 new homes alongside a hotel, gym, shops, supermarket and restaurants. Director Yuan Sun said: “We have seen significant tangible benefits of using modular build. In addition to building homes quicker, it gives more time-certainty. In Lu2on phase 1, several bathroom pods were already built within six months of launching construction work. We are now exploring other elements of modular construction for Lu2on phase 2.”
NU living, part of housing association Swan Group, has been an early adopter of modular methods, with its own factory supplying new homes in Essex and east London. Beechwood in Basildon will deliver 750 units with two, three, four or five bedrooms. 200 have already already built, most in ‘affordable’ housing for rent or to purchase. Purchasers can design the layout and specification of their home using an online configurator, with their personalised property then being made to measure at the factory and delivered to the appropriate plot.”
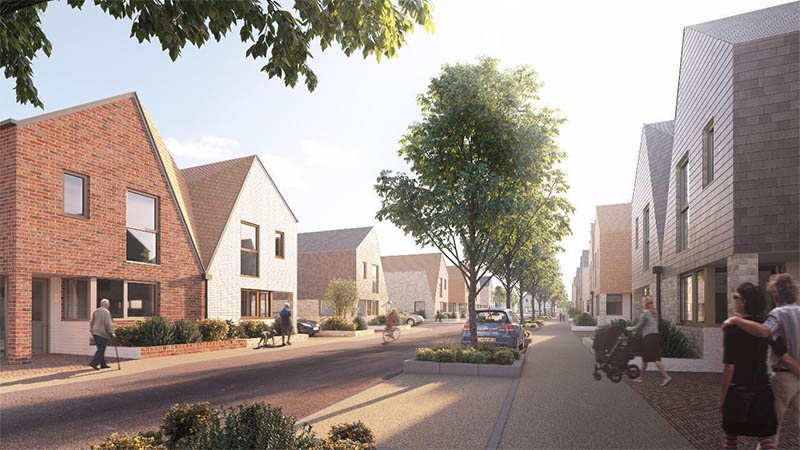
An increasing number of housebuilders and housing providers are setting up their own facilities in the modular world for all or part of their homes. Weston Homes launched its £12m Braintree Logistics Centre in late 2018. “Within the next 10 years, technology will allow for new homes to be fully manufactured offsite by robots and computer-assisted engineering tools; customer specification choices fully automated; with factory-made components then built onsite using machines like a highly advanced Lego system,” said chief executive, Bob Weston.
Legal and General have ambitious targets, with modular construction playing a significant part in achieving them – their factory outside Leeds can build up to 3,500 new homes every year, from affordable starter homes to retirement living. The have even set up a Modular Academy to teach all aspects of building this way. Rosie Toogood, CEO of Legal & General Modular Homes, said: “What we are doing at Legal & General Modular Homes is groundbreaking. We have taken a high-tech engineering approach to developing our product range, designing and manufacturing homes in a truly innovative way that will transform the way homes are built in the UK.”
Countryside already has a factory in Warrington and plans to open two more in the next two to three years, one in the Midlands and one in the South East. Units are delivered onsite with plumbing and electrical channels installed, windows in place and insulation. “We're very focused on modern methods of construction,” said the company’s housebuilding chief executive Phillip Lyons said. “We wanted to bring our activity in-house and the Warrington factory is not a trial, it's the real thing. We intend to roll it out across the UK.”
Ideal Modular Homes last year opened a 150,000 sq ft factory in Speke which will deliver up to 500 new homes per year. The construction process here can complete a two-storey family house in four working days. CEO Luke Barnes said: “Factory-made homes are faster to produce, better for the environment and once sited, are cheaper to run and more energy efficient. This is housing at its most advanced. Although the UK has been slow to adapt to change, if we continue to support modular construction as a business model, we will begin to see the housing gap close.”
Environmentally friendly homes manufactured offsite are not exclusive to homebuyers. Last year, homelessness charity Centrepoint announced plans to build 300 modular homes by 2021, to help young homeless people in Great London and Greater Manchester. Each complete home will cost just £50,000 to build.
Take a look at some examples of modular homes:
Positive Homes: The Newlands, Newark, has three-bedroom homes from £175,000.
Zebra Homes: Great Bentley, Essex, has four-bedroom detached houses from £450,000.
Keepmoat Homes: The Mallards, Swanley, Kent has the final two-bedroom homes from £350,000.
The Wee House Company
Flagship Group.
WeberHaus in Germany.